Key points of lubrication for steel plant equipment
May 27,2021
The lubrication conditions in the metallurgical industry are complex, and compared to other industries, the consumption of lubricants is high. Metallurgical equipment mainly includes sintering equipment, ironmaking, steelmaking and non-ferrous metallurgical equipment, and pressing equipment. The lubricating oil for steel production equipment has many special features, especially for large complete sets of equipment, which have a high degree of automation, need to withstand heavy loads with impact, high working temperature and high movement speed. Some outdoor operation equipment operates in harsh environmental conditions, with high dust, humidity, and easy corrosion. Therefore, there are high requirements for equipment lubrication and oil.
1、 Lubrication of sintering and related equipment
Such as open hearth furnaces, blast furnaces, converters, coking machines, coke pushing machines, large blowers, transport machines, etc., are mostly exposed to dust, smoke and other environments, and are prone to corrosion, abrasive wear, cavitation, pollution, etc. The lubrication of gears, bearings, reduction systems, hydraulic systems, etc. in these devices also has their corresponding characteristics.
1. Sintering equipment
Limestone and ore sintering equipment often operates in dusty, diagnostic, and high-temperature conditions, so the lubrication of their bearings requires the use of composite lithium based, bentonite based, or composite aluminum based grease.
2. Coking equipment
Due to long-term exposure to an environment permeated with coal powder, it is necessary to ensure good sealing and lubrication. For example, the hydraulic systems of furnace door opening and closing bottom turning cars and water spray rapid cooling cars generally use flame-retardant hydraulic fluids such as water/ethylene glycol, and conveyor bearings need to be lubricated with lithium based or composite calcium based grease.
3. Pushing equipment
Intermittent work, with impact loads, in coal dust and high temperature environments, requires the use of heat-resistant and water-resistant extreme pressure lithium grease or the use of anti-oxidation, anti rust or extreme pressure lubricating oil for lubrication. The hydraulic system should also use flame-retardant hydraulic fluid.
4. Furnace top equipment
Large blowers, ore bucket towing wire ropes and other furnace top equipment can generally be lubricated with a 0 # or 1 # extreme pressure lithium based grease dry oil lubrication system, and the furnace top machinery can use phosphate ester flame retardant fluid as the hydraulic medium. The load of the molten iron ladle is high and the temperature is high, so it needs to be lubricated with high drop point extreme pressure composite lithium grease.
5. Gas purification and chemical byproduct equipment
These devices are often affected by dust and corrosive smoke, so the lubricant used for gas delivery machines should be anti-oxidation and rust proof turbine oil, and a circulating lubrication system with filters should be applied to strengthen oil pollution control.
2、 Lubrication of steelmaking equipment
Steelmaking equipment includes open hearth furnaces, converters, mixers, and cranes. Modern steelmaking equipment requires corresponding lubrication systems and the use of appropriate lubricants to avoid equipment downtime caused by abnormal lubrication.
1. Oxygen blown converter
The oxygen blowing converter equipment is supported by a limit rotating shaft, and the supporting rolling bearings are usually lubricated with molybdenum disulfide lithium grease or extreme pressure composite lithium grease. Static pressure bearings and PTFE shaft pads can also be lubricated with grease. Lubricating oil for medium or heavy load industrial gears used in converter drive. There are many lubrication points for the main auxiliary equipment such as exhaust fans, motors, loading cranes, and hoists, which are lubricated with corresponding grease and dry oil lubrication systems. The driving gears are commonly lubricated with oil baths.
2. Continuous casting machine
The rolling bearings used in continuous casting machines are under high temperature conditions and are generally lubricated with composite aluminum based grease. The lubrication of the mold adopts lubricants that prevent mold wear or adhesion. Water/ethylene glycol or phosphate ester type media are commonly used as hydraulic media for continuous casting. The main function of continuous casting is to connect the past and the future, so the lubrication of continuous casting related equipment should be stable and reliable, and automatic control equipment should be used as much as possible. If a certain steel plant adopts oil air lubrication to lubricate and cool the roller bearings, transition roller bearings, and pull roller bearings, it improves the cooling and sealing effect of the bearings and extends their service life.
3、 Lubrication of steel rolling equipment
The steel rolling equipment mainly includes hot rolling mills and cold rolling mills. Due to the significant differences in the structure and lubrication requirements of various steel rolling mills, different lubrication systems and methods are adopted on the steel rolling mills. Due to the complex structure of modern rolling mills, their lubrication parts include the working machine base, universal joint shaft and its balancing device, gear machine base, main coupling, reducer, coupling and motor, as well as front and rear coilers, uncoiler, etc. Therefore, currently, dry oil or thin oil centralized lubrication systems are commonly used.
1. Dry oil lubrication
Dry oil centralized lubrication refers to the centralized pumping lubrication method commonly known as grease lubrication for rolling bearings. The selection of lubricating grease needs to be based on different working conditions to choose the appropriate grease for the bearings on site. For example, currently, No.1 and No.2 extreme pressure composite lithium based grease are commonly used.
2. Thin oil circulation lubrication
The thin oil station is the heart of the thin oil circulation lubrication system, which is responsible for forcibly pressing lubricating oil to the friction parts of the machine. The rolling mill oil film bearings in steel mills use this method. The lubrication system of rolling mill oil film bearings includes dynamic pressure system, static pressure system, and dynamic static pressure hybrid system. The liquid friction condition of dynamic pressure bearings can only be formed when the rolling mill has a certain rotational speed. When the rolling mill starts, brakes, or reverses, its speed changes cannot guarantee the conditions of liquid friction, which hinders the use range of dynamic pressure bearings. Static pressure bearings rely on static pressure to keep the shaft neck floating in the bearing. The formation of high-pressure oil film is independent of the speed, and can ensure liquid friction conditions during start-up, braking, reverse rotation, and even static operation. They have high load-bearing capacity and good rigidity, and can meet any load and speed requirements, but require a dedicated high-pressure system, which is costly. So, use a static pressure system to supply high-pressure oil during startup, braking, reverse rotation, and low-speed operation. But when driving at high speeds, the static pressure system is turned off, and the dynamic static pressure hybrid system that uses the dynamic pressure system to supply oil has a more ideal effect. The lubrication characteristics of the rolling mill oil film bearing determine that the oil film bearing must meet its performance requirements in order to ensure the normal operation and continuous production of the rolling mill. Therefore, the oil film bearing oil needs to have the following characteristics:
(1) Excellent viscosity temperature performance; (2) Excellent emulsification resistance, able to quickly separate water from oil during long-term use; (3) Good anti-wear and extreme pressure performance; (4) Good anti-wear, anti rust and anti foam performance to prevent the lubrication system from rusting, blocking the oil circuit, causing wear and insufficient oil supply; (5) Good oxidation stability, cleaning and filtering properties ensure smooth oil flow in the lubrication system and normal lubrication.
3. Lubrication of bearings for high-speed and high-precision rolling mills
The bearings of high-speed and high-precision rolling mills are lubricated with oil mist and oil air lubrication.
The competition in the modern steel metallurgy industry is becoming increasingly fierce, and at the same time, it is limited by energy-saving and environmental protection policies, as well as the impact of self operated shortages and price increases. Therefore, the economic benefits contained in carrying out equipment lubrication management are particularly important. The lubrication technology and management methods implemented have the potential to reduce the cost of spare parts for motion pairs and the entire machine, as well as decrease inventory funds; Reduce maintenance accidents, maintenance personnel, and maintenance costs; Reduce energy consumption and save resources; Improve production efficiency, etc.
PREVIOUS:
Related Posts
May 27,2021
Contact Us
E-mail :
smjx@smodm.cn
Phone/WhatsApp:
+86-13915240746
Address:
No.1 Aquatic Farm, Weichang Village, Ligang Street, Jiangyin City, Jiangsu Province, China
Wechat:
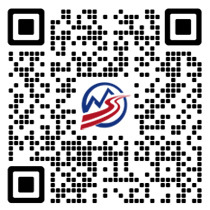