Controlled cooling process for high-speed wire hard wire production
May 27,2021
1 Preface
In the wire production industry, wire rods made of medium to high carbon steel with a carbon mass percentage of not less than 0.45% in high-quality carbon structural steel are commonly referred to as hard wires. Hard wire is a raw material used for processing low relaxation prestressed steel wire, steel wire rope, steel strand, tire steel wire, springs, etc. At present, domestic hard wire generally has problems such as low Soxhlet formation rate, poor plasticity, high strength, and surface defects, which seriously affect the first drawing performance. Therefore, studying how to develop reasonable cooling control processes in actual production, effectively controlling the quality and performance of hard wire products, has positive significance.
The influence of heating conditions on performance
Under the same post rolling controlled cooling conditions, the heating temperature and heating time of the steel billet directly affect the microstructure and properties of the hard wire, and this effect is significant. The temperature measurement on the rolling line reflects that with the increase of rolling passes, the temperature of the rolled piece tends to be consistent for steel billets with different exit temperatures. Both the inlet temperature of the precision rolling and the wire feeding temperature are basically the same. This indicates that the effect of heating temperature on the microstructure and properties of hard wire is not due to its influence on the final rolling temperature, but rather due to the changes in the microstructure transformation mechanism during the cooling process of the rolled wire caused by different heating conditions. Firstly, high heating temperature or long heating time will cause the initial austenite grains of the steel billet to coarsen before rolling, and the large initial grain size will inevitably lead to larger recrystallized grains of the high-temperature wire rod after rolling. Secondly, compared with low-temperature rolling, the number of deformation dislocations in the microstructure of the rolled wire is relatively reduced after high-temperature rolling. Under the same final rolling temperature and post rolling controlled cooling system, the relative coarsening of austenite and the reduction in the number of deformation dislocations will lead to a decrease in the transformation temperature of various structures during the cooling process, and an extension of the incubation period. This is manifested in the downward movement of the continuous cooling C curve to the right and downwards, while the downward movement of the ferrite curve is particularly prominent, which greatly increases the possibility of ferrite precipitation at the same cooling rate. The transformation of ferrite preferentially nucleates at austenite grain boundaries. Due to the coarse austenite grains before the transformation, the grain boundary area is relatively reduced, making it easier for the preferentially precipitated ferrite to form a network. In addition, the high heating temperature and long heating time of steel billets can intensify decarburization of the steel skin, and the carbon concentration at a certain depth on the surface of the wire rod may relatively decrease, which may also lead to an increase in the precipitation of ferrite.
3. Cooling control after rolling
In steel rolling production (hot rolling), the products produced must be cooled from the high-temperature red hot state after hot rolling to room temperature. The cooling process at this stage will have an extremely important impact on the quality of the product. Therefore, how to carry out post rolling cooling of wire is one of the key links in product quality control throughout the entire wire production process.
Controlled cooling is the use of residual heat from rolled steel to provide a certain cooling rate and control its phase transformation process, without the need for heat treatment. The purpose of controlled cooling of high carbon steel wire is to simulate a lead bath quenching process, so that the wire can obtain a martensite structure with good comprehensive mechanical properties (good tensile strength, high strength, and high toughness). The controlled cooling of wire after rolling is divided into two stages: forced cooling in the water-cooled section and phase change cooling in the air-cooled section. The controlled cooling process consists of a water cooling zone and an air cooling zone. After the wire is cooled to a certain temperature by water, it is spun to form a dispersed coil of straight wire distributed on the air-cooled line for air cooling.
Design of 4 Control Cooling Process Parameters
The controlled cooling of wire is mainly a heat treatment process aimed at changing the metallographic structure and improving the drawing performance, so the theoretical basis for the design of controlled cooling process parameters is the "C" curve. The parameters that need to be controlled in the cooling process are mainly the final rolling temperature, wire drawing temperature, cooling rate (or cooling time) in the phase transition zone, and coiling temperature. These parameters are the key to determining the final quality of wire products.
4.1 Final rolling temperature control
Due to the influence of austenite grain size on the microstructure transformation and morphology of transformation products during phase transformation, it is meaningful to control austenite grain size by controlling the final rolling temperature. The control of final rolling temperature can be achieved by increasing or decreasing the amount of water cooling between the rolling mill stands and the amount of water in the front water tank of the rolling mill. After the final rolling temperature is determined, the cooling method of the nozzle must be considered for large-diameter high carbon steel wire. The selection of the water tank should be as far away from the wire spinning machine as possible, so that the water-cooled wire can have a longer temperature equalization time. When the wire enters the air cooling section, the temperature on the entire section is basically uniform, avoiding incomplete temperature equalization during the air cooling process, prolonging the time to complete phase transformation, increasing the difficulty of cooling control, and even producing abnormal structure.
4.2 Silk spinning temperature control
The spinning temperature is a key parameter for controlling the starting temperature of phase transition. The number of cooling stages affects the temperature of silk spinning, which in turn affects the grain size of austenite and indirectly affects the position of the cooling transformation curve. In theory, choosing a higher spinning temperature will result in the wire remaining in the austenite structure after spinning, and carbon and other accompanying elements will still be solid dissolved in the austenite. The elongation of austenite grains increases the undercooling of austenite on the air-cooled line, causing the continuous transformation curve to shift to the lower right. The transformation of coarser austenite grains into pearlite occurs at lower temperatures, resulting in a decrease in interlamellar pearlite and an increase in the austenitization rate. Choosing a lower spinning temperature results in finer austenite grains, increased grain boundary area, more nucleation points for pearlite, and smaller pearlite spheres in the wire, which improves the plasticity index of the wire. At the same time, a lower spinning temperature combined with rapid air cooling can suppress the precipitation of ferrite, reduce the content of ferrite, and improve the morphology of ferrite. According to the C-curve graph, in order to achieve a high Soxhlet transformation rate for hard wire, the cooling rate must reach 10-15 ℃/s.
A large number of experiments were conducted to determine the spinning temperature of HeHua. The spinning temperature ranged from 820 ℃ to 930 ℃, and the steel grade was 60 # steel with the highest selection for air cooling. The experimental results indicate that:
(1) The rate of Soxhlet formation is not closely related to the spinning temperature, but to the cooling rate of air cooling after spinning. Due to the adoption of maximum air cooling, the Solzhenization rate is relatively high, approaching 75%.
(2) As the silk spinning temperature increases, the strength index also rises; The spinning temperature decreases, and the plasticity index increases
(3) Based on the above experimental results, we selected a spinning temperature of 850 ℃ -850 ℃ for the production of hard wire, turned on all the air and cold fans to the maximum, and set the roller speed at 1.0m/s. In order to achieve better plasticity indicators, elongation at break, and surface quality. Subsequently, we randomly conducted tracking tests on 10 furnace numbers of 60 # steel, and the results are shown in Table 1.
4.3 Control of cooling rate in phase transition zone
In order to achieve performance similar to lead quenching treatment for high carbon wire, Stelmor should use standard cooling. The control of cooling speed mainly involves controlling the speed of the cooling fan and roller conveyor.
4.3.1 Determination of speed of air-cooled roller conveyor
The speed of the Stelmor roller conveyor can be determined by the following equation:
In the formula C=W · V/(π · d), C represents the roller speed, m/s; W - wire ring spacing, mm; d - wire ring diameter, mm;
V represents the rolling speed, m/s。
The roller speed is determined by the distance between the wire rings, the diameter of the wire rings, and the rolling speed. Given the final rolling speed, the diameter of the wire loop is also determined, and the roller speed depends on the distance between the wire loops. The selection of wire loop spacing is related to the diameter of the wire. A large diameter requires a large spacing between wire loops. Generally, different diameters correspond to an optimal spacing between wire loops. If the spacing is smaller than this, it will affect the cooling effect. If the spacing is larger than this, as the spacing value continues to increase (taking into account the length factor of the air-cooled section), slightly increasing the relative velocity between the wire and the flowing air has little effect on the strength of the wire. During rapid cooling, the roller speed should be able to ensure that the distance between adjacent loops is greater than 40mm, in order to obtain the required cooling speed for obtaining fine pearlite [4]. Practice has shown that when the spacing is 40mm, the heat between adjacent wire loops has little effect on each other, and the cooling rate is mainly controlled by the air volume. The spacing value of 40mm is the control limit value of the standard cooling process parameter - roller speed. In addition, the speed of each section of the transport aircraft should be gradually increased to ensure that the overlapping points of the loop edges are staggered, eliminate the influence of hot spots, and improve the uniformity of the same circle strength. Prevent the formation of pre eutectoid Fe3C in high carbon steel wire at lower cooling rates, which is not conducive to drawing.
4.3.2 Selection of Cooling Fans
The selection of cooling fans includes two aspects, namely the determination of fan air volume and the number of fans.
⑴ Distribution of cooling air volume
For large-diameter high carbon steel, in order to increase the cooling rate and undercooling of austenite before phase transformation, the fan must be fully turned on. When the wire is ejected from the spinning machine and scattered on the Steyr transport machine, it is in a state of being sparse in the middle and dense on both sides, resulting in different cooling rates between the middle and edges. Although the distribution of wind nozzles on the transport aircraft enhances the cooling capacity on both sides, in order to minimize the dispersion of performance in the same circle, it is necessary to use an air volume adjustment device to optimize the distribution of air volume.
Determination of the number of fans
The number of activated fans should take into account the influence of wire temperature and roller speed. Generally speaking, as the spinning temperature increases, the undercooling degree of austenite increases, and the completion time of phase transformation is long. In order to ensure that phase transformation occurs in the air-cooled section, it is necessary to increase the number of fans used. Similarly, the determination of the number of fans is also related to the speed of the roller conveyor. When the final rolling speed is constant and the roller conveyor speed is fast, the number of fans required to be used is relatively increased. Due to its high enthalpy, large-diameter high carbon steel wire rods must increase the roller speed to eliminate interference between hot spots in the wire loop in order to improve cooling speed at the same final rolling speed. Therefore, the number of fans used should also be increased accordingly [5]. For different specifications, corresponding to different rolling speeds and wire feeding temperatures, the key fans used for phase transition should be determined.
4.4 Control of Rolling Temperature
The temperature of the coil depends on the cooling process after the phase transition is completed. In order to ensure product performance, avoid high-temperature oxidation after coiling, and improve the working environment, it is generally required to coil at temperatures below 250 ℃. Sometimes, due to limitations in cooling conditions, the temperature of the coil may be higher, but it should not exceed 350 ℃ at most.
5 Production Status
The fourth high-speed wire production line of Beigang has rolled hard wire varieties such as 45 #, 55 #, 60 #, and 65 # since the production of steel products. The dimensional tolerance of the wire rod is controlled within the C-level standard range, and the main product 45 # (Φ 6.5mm) has a tensile strength of 820-900MPa; The shrinkage rate is over 40%, and the Soxhlet transformation rate is over 70%,; And there is no reticular ferrite tissue; Randomly test the performance of 45 # and Φ 6.5mm in 10 furnaces, and the results show that the strength deviation is mostly within ± 50MPa, and the surface shrinkage deviation is within 6%, as shown in Table 2.
6 Conclusion
After the control of the cooling process mentioned above, the surface quality and continuity of the hard wire products produced by the fourth high-speed wire production line of Beigang have reached a high level, and the martensite content is high. However, at the same time, it is necessary to continuously optimize the cooling process parameters and produce high-quality wire that meets the requirements of different users.
NEXT:
Related Posts
May 27,2021
Contact Us
E-mail :
smjx@smodm.cn
Phone/WhatsApp:
+86-13915240746
Address:
No.1 Aquatic Farm, Weichang Village, Ligang Street, Jiangyin City, Jiangsu Province, China
Wechat:
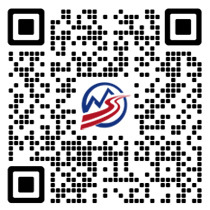